真空熔覆镍基合金碳化钨耐磨涂层的研究
2015-6-4 9:07:55 点击:
【摘要]为了提高零件表面的硬度和耐磨性,使用真空熔烧法,在45#钢上涂覆1层碳化钨耐磨涂层,并通过显微硬度计和耐磨试验得到了 WC耐磨涂层不同深度的硬度分布及耐磨性变化数据。结果表明:涂层中扩散层部分的硬度最低,涂层的硬度 较基体和扩散层都有较大的提高,而且涂层部分不同深度硬度变化不大;在干摩擦条件下,涂层最外层的耐磨性最好,中间几层的耐 磨性能相当,靠近扩散层处的涂层的性能最差。
[关键词]真空熔烧法;镍基合金;碳化钨;显微硬度;磨损量
0引言
磨损是材料三大主要失效形式之一,它造成的经济损失是十分巨大的,粘着磨损是最常见的磨损形式之一,它的发展十分迅速,容易使零件或机器发生突然事故,造成巨大损失。磨损失效的各类零件中起因于粘着磨损的大约占15%,而影响固体材料粘着磨损的主要因素之一是材料的硬度,对摩擦副材料的硬度而言,材料的硬度越高,耐磨性越好,因此,研究零件材料的硬度和耐磨性有着重要的现实意义。另外,使用表面工程技术,可使材料表面获得它本身没有而又希望具有的特殊性能(如要求表面耐磨性好,心部韧性好),而且表层很薄,用材十分少,性能价比高,节约材料和节省能源,减少环境污染,是实现材料可持续发展的一项重要措施。正是在这样的背景下,本文试图使用试验的手段,对真空熔烧法制备所得的镍基合金碳化钨(WC)耐磨涂层的硬度及耐磨性作一些研究。
1试样制备与试验方法
1.1 试样的制备
将镍基碳化钨合金粉末FN15-WC35和镍铬自熔合金Ni45B按3:1(质量比)的比例混合均匀,然后加饱和松节油,将混合后的粉末调制成膏状备用。粉末成分见表1。用煤油将要涂覆层的45钢表面清洗干净,并在电烤箱中烘干,检查涂覆的耐磨涂层是否存在缺陷。如有涂覆不足或涂层有流失处,一定要进行补涂,以保证涂层比较平整,不能存在缺陷。涂覆好后再放入电烤箱中进行烘干,烘干温度为110℃,烘干时间应大于8h,使得涂层不易剥落。
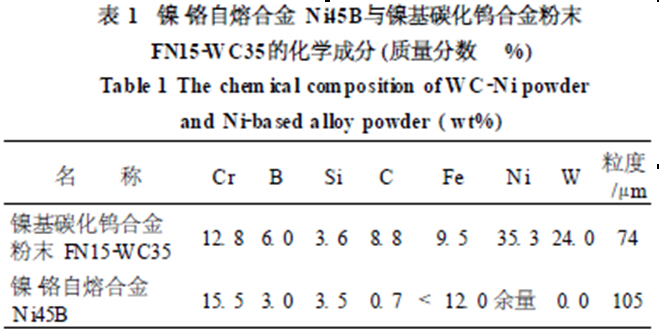
上图镍铬自熔合金NI45B与镍基碳化钨合金粉末FN15-WC35化学成分质量分数
将涂覆好合金粉末的45#钢试样放在真空炉中熔烧,熔烧温度为1150℃,此温度比镍基合金的熔点高约30℃,使涂层合金处于熔融状态。熔烧时炉内真空度要保持在50Pa以下,避免合金在高温下发生氧化。然后将涂层表面手磨床磨平和抛光。
1.2洛氏硬度的测试
1 2 1测量涂层表面和基体的硬度
测量涂层的洛氏硬度的目的是为了与其它金属材料的硬度进行比较。被测量涂层面为涂层表面,被测量基体为距离结合界面大于3mm处基体。测量时将试样从中间剖开,切开截面作为测量表面。使用的硬度计为CHX-1型显微硬度计,每个值测 量5个点,后取平均值。测量硬度载荷为300N,保压时间为 5 s。测量结果见表2。
表2镍基合金涂层与基体的洛氏硬度
Table 2 HRC hardness of Ni-base coating and substrate
材料 测量值 平均值
涂层 59. 8 60. 4 62 7 56 3 55. 9 59. 0
基体 22 6 21. 7 19. 6 18. 5 23. 1 21. 1
1 2 2测量涂层到基体的显微硬度分布
仍然使用CHX-1型显微硬度计,测量涂层不同深度的硬度 值,每个深度测5个点,然后取其平均值。测量硬度载荷为 300N,保压5s,从涂层表面向基体以0 1为1个步长。测量时若测量点正好在缺陷处,则删除该点,另补加1个点。测量结 果见图1。
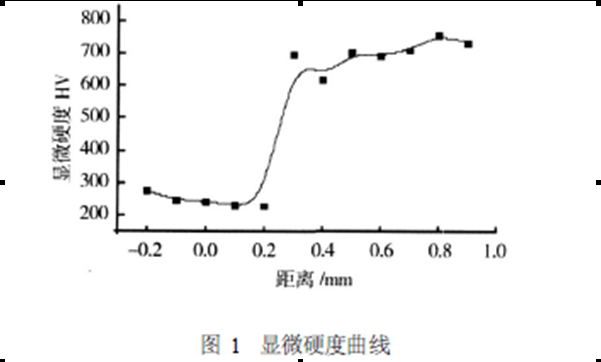
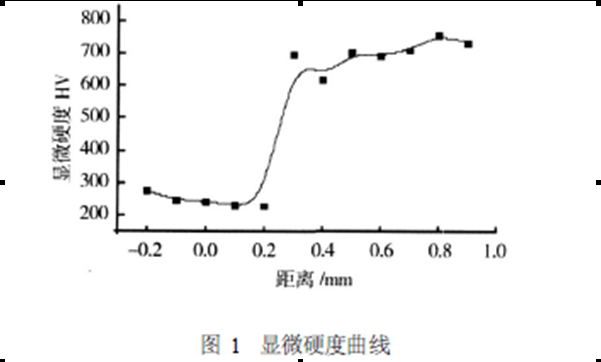
Figure 1 Micio-hardnessofNi-base alloy coating along the depth
1.3磨损性能试验
磨损试验是在MPX-2000A盘销式磨损试验机上进行的。 涂层盘式样是将熔烧后的镍基合金涂层试样进行加工,将式样涂层表面磨削加工至Ra=1.6。盘试样为被测磨损件。每测定完1层后,将磨损后的试样表面再磨削加工,将磨损部分去掉,同时再磨削出另1层Ra= 1. 6的磨损面,依次进行不同深度的磨损性能试验。现假设以过渡层与基体的结合界面为0界面, 正方向指向涂层表面,分别测量5种不同深度的耐磨性,深度分 别为0.76、0.64、0.49、0.36、0.2mm。5种深度的磨损试验均在相同的试验条件下进行:转速为1 100r/min(相当滑动速度是 1. 5m/s),载荷为50N,无润滑干摩擦状态。应用称重法检测磨损量,磨损量的测量是用TG328A型电子分析天平,精度为10-4 g。每隔2h称被测磨损件的质量,每次测量5次,取其平均值,每组试样总的磨损时间为22h,取其前10h的变化。销试样作 为对磨件,采用淬火工具钢(HRC55~60),它的直径为<5mm。试验结果见图 2。
2试验结果与分析
2 1碳化钨耐磨涂层硬度分析
由表2可知,涂层的硬度要远大于基体部分的硬度,涂层对基体的性能有1个很大的提 高。图1是从基体到涂层不同深度的显微硬度分布曲线。由图 1可知,涂层在扩散层部分的硬度最低,由于扩散层是1个在熔 烧过程中形成的高铁的单相组织,硬度较低,但是扩散层的耐蚀 性很好。而涂层部分由于分布有块状的WC颗粒和WC与合金元素形成的块状复相化合物(见图3),而这些颗粒的硬度都远大于扩散层组织的硬度,使得涂层部分具有很高的硬度。由 图1曲线可知,从基体到扩散层有1个略微下降的趋势,这是由于熔烧过程中元素的扩散使得基体靠扩散层部分的硬度有所增 加,而扩散层是较软的高铁单晶组织。
从扩散层到涂层部分曲 线几乎成直线上升,这说明涂层部分的硬度要优于扩散层;且在 涂层部分,涂层硬度有上下起伏,这是由于WC颗粒在测量部分 的分布并不是十分均勻造成的,在涂层表面处的硬度比涂层内 部高,这是由于在熔烧时,WC在表面附近的“偏聚”造成的。
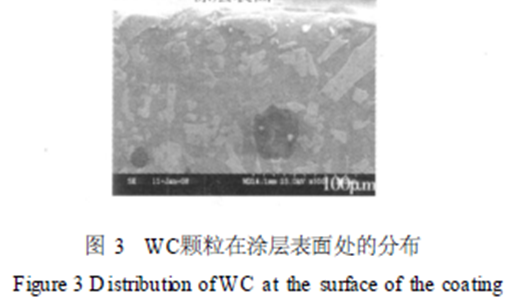
图(3)碳化钨颗粒在涂层表面的分布
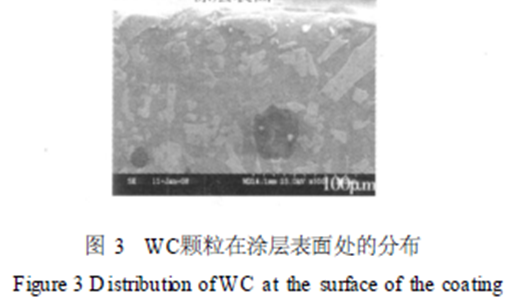
图(3)碳化钨颗粒在涂层表面的分布
2. 2涂层耐磨性分析
由图2中干摩擦测试结果的试验曲线可知,涂层在最外层 的磨损量最低,中间3层的变化量相差不大,最靠近界面层的磨 损量最大,且在磨最里层时,磨损试验机震动较剧烈,磨损量加大。在同等条件下,如果对淬火45#钢进行磨损试验,则机器震 动剧烈,基体表面大片脱落,同时发出刺耳的噪声,磨损试验无 法继续进行。可见涂层的耐磨性要远比基体材料的耐磨性好。
涂层的耐磨性较好的原因是:涂层所用的镍基合金为低熔点自熔镍基合金。为了降低镍基合金的熔点,在其中加入较高含量Fe和Ni,还能溶解一定量的Si形成固溶体,根据X射线衍,射结果,在涂层中Ni是以Ni3Si2、Ni4B3、NiSi化合物、Ni16Cr6Si7 复相化合物和Ni29Cr07FeQ 36共晶的形式存在,而且这些化合物具有较高的硬度,它们对合金组织起固溶强化和弥散强化的作用,在镍基合金中,Si大部分溶于Ni奥氏体中,起固溶强化作用;B除少量溶于Ni奥氏体中,大部分以金属间化合物的形式弥散在合金中,起弥散强化作用.另外,合金中的Cr也 是以CeBC4和CrB化合物的形式存在,并且同样弥散在涂层中起固溶强化和弥散强化作用。再者镍基合金共晶组织有较高的 韧性,在摩擦时,磨损表面不易产生裂纹和剥落。
由于在镍基合金中加入一定量的WC硬质相,WC是1种硬度高耐磨性好的材料。合金耐磨涂层材料在磨损时,合金基体材料主 要起支撑和粘结硬质相的作用,而硬质相是抗磨的主体,它们抵 御外来坚硬磨料嵌入基体,并能够有效地将部分磨料在涂层表 面的滑动运动和犁削变为滚动运动,部分磨料在涂层表面滚动,增大接触面积,减小接触面的正应力,起到保护摩擦表面的作用。同时硬质相也能有效地阻挡表面裂纹的萌生和扩展。 再者,WC与基体的结合强度也直接影响涂层的耐磨性,因此,在镍基合金中加入的硬质相是Ni包WC粉末,克服了普通 WC颗粒与镍基合金基体间浸润角小的缺点,在熔烧时使得WC 颗粒与基体合金粘合性增加,而且在磨损试验时,没有发现有 WC颗粒剥落现象。
最外层之所以具有最好的耐磨性,是因为在熔烧过程中,WC颗粒有“上浮”见象,在涂层表面附近WC分布较内部密集,而WC及其与合金元素形成复相化合物是抗磨的主体,且此处 涂层的硬度较涂层内部要高,故最外层具有最好的耐磨性。
中间3层的耐磨性差别很小,这是由于在涂层内部WC分 布较均匀,且涂层内部组织类似,故耐磨性差不多,由图2中曲 线可知,越靠近涂层外测,耐磨性越好,但在内部不同层的耐磨 性相差并不大,这有利于涂层的应用,当1层涂层被磨损时,可 通过将磨损层加工掉,继续使用里面的层作为功能涂层使用。
最里层的耐磨性最差,从图2中曲线可以看出在磨损的前几个小时里,该层的耐磨性与之前的几层相差不多,但后面几个小时涂层的磨损量突然增大,这是由于涂层磨损到了扩散层,扩散层相对于涂层来说,硬度要小,相对较软,故磨损量增大,但由于扩散层组织较致密,虽然软,磨损量的增加值并不是很大。
3结论
1) 涂层中扩散层部分的硬度最低,基体靠扩散层侧的硬度 较扩散层略有上升,但变化不大,这是在熔烧过程中涂层向基体的元素扩散造成的。
2) 涂层的硬度比基体和扩散层硬度都大,这是由于涂层中 弥散分布的WC以及WC和涂层元素发生反应产生的块状复相化合物造成的。
3) 由于块状硬质相在涂层中分布较均匀,涂层部分硬度变化不大。
4) 在干摩擦条件下,涂层最外层的耐磨性最好,中间几层 的耐磨性能相当,靠近扩散层处的涂层的性能最差。
- 上一篇:碳化钨涂层加工异形耐磨件 2016/8/10
- 下一篇:耐磨涂层的分类及实际应用案例 2013/8/30